MKL’s ’98 1200C – Y2K Performance Project – S/E Heads & Dyna 2000i Ignition
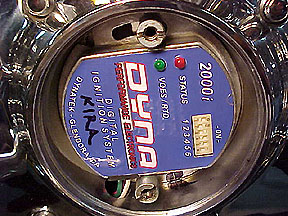
The Self-Contained Dyna 2000i Adjustable-Curve Single-Fire Ignition Module 2/00
This project was designed to further increase the bike’s entire powerband, specifically the mid range. First, some background-
Installation: All parts for this project were installed by the local HD stealership. I decided to take advantage of the 20% off parts sale they were having, and since I had to have my top end ripped off anyway (base gasket leak covered under warranty,) I decided to have them put the new S/E Dual-Plug High-Compression Heads and Dyna 2000i Ignition System on in place of the old stock components. Initially, the deal seemed good, as I paid for nothing but the discounted parts, the warranty deductible ($50), and only 1 hour labor to set up the ignition. Without getting into the messy details, they did an extremely poor job of installation (among many other things, the base gaskets blew within 10 miles, hardware was missing, and absolutely no effort was put into fine tuning the engine for the new components). Suffice it to say (with respect to tuning) that all work was done by me. I performed the timing and carburation as required from scratch once the top end was reassembled (following the aforementioned base gasket blowout) – This tuning is the tricky part, and it did require some trial and error. Here is what I found, and my impressions of the setup thus far:
Dynatek 2000i Ignition Module with Dynatek DC6-4 Coil: As part of my upgrade, I wanted to switch over to a single-fire ignition system which was self-contained, offered adjustable curves, was easy to install and adjust, and was relatively affordable. This new Dyna unit was the perfect candidate in all regards. It offers 4 different advance curves to select from, as well as the ability to select between single-fire and dual-fire at the flick of a switch. In addition, the redline is adjustable between 6,000-7,500 rpm, and the VOES can be retarded (VOES wire grounded) for extreme (artificial breathing) applications like Nitrous Oxide or Turbo Kits. Hey, you never know… 😉 Click here for a picture of the chart you use to adjust the ignition module – you simply turn the 6 tiny switches on the module “on” or “off” to manipulate the settings. The Dyna DC6-4 Coil was also a perfect choice for my application – All four towers required are housed in one enclosure, which fits neatly into the stock location using the stock mounting bracket, with no further modifications required. The only downside is my old chrome coil cover doesn’t fit it. The coil is pictured below…
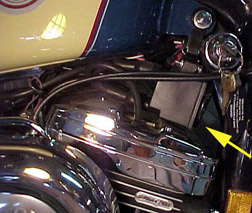
The Dyna DC6-4 High-Performance Four-Tower Single-Fire Coil 2/00
Setting the Timing: Static timing is made easy with this module. Essentially, per the instructions, you simply line up the TDC mark in the timing inspection hole (on the compression stroke of the front cylinder). Once you do this, you start at extreme left and turn the module clockwise slowly. At the very position the red LED on the module shuts off, you lock down the module’s position. Quite easy, actually, and it’s all detailed well in the instructions. From there, you can proceed to dynamic timing per the instructions – there was no change necessary on my motor. However, here’s an interesting thing to note: Look at the module’s position as shown in the above picture, as it’s properly locked in and marked. There’s not much play involved at all! In fact, if I wanted to retard the timing even slightly from static optimal, it would be impossible to rotate counter-clockwise more than ~2 degrees, because the module itself hits the two adjustment screws! This is something that would definitely interfere with some high-compression / built motor applications, where even the least aggressive advance curve (#4) is too advanced, and the timing can’t be retarded to compensate!
Selecting the Proper Advance Curve: Click here for a chart of the Dyna 2000i’s available curves. For reference, Buzz Buzzelli writes in his “Harley-Davidson Sportster Performance Handbook” that “Extensive testing has also shown that both Stage I and Stage II motors run best if the ignition timing at idle is set at about 10-12 degrees before TDC, is advanced to near 22-25 degrees at 2,000 rpm, and reaches full advance (my note: I believe this is ideally 28-30 degrees) at 3,250 rpm.” Back to my Dyna – Per the instructions, you start in the middle (Curve #2) and see what works. If it pings, select a more moderate curve, and if it doesn’t ping, select a more aggressive curve. It’s a trial and error job. In my application, here’s what happened: Around town (speeds generally under 50 mph, gears 1-4), no matter how much I beat on it, I could run the bike at the most advanced curve (#1) with very minimal pinging, or at curve #2 with no pinging. The highway was a different story. Running the bike on the highway at Curve #1 made the engine ping like a Chinese phone book, no matter how much you babied the throttle. Curve #2 wasn’t much better. Curve #3 was tolerable, but no that great (about the same level of pinging as an absolutely stock bike), and Curve #4 was finally acceptable. Trouble is, the bike’s acceleration, which was ferocious around town in Curve #1, was now hampered by this moderate Curve #4. But, unless I wanted to pull over and adjust the curves based on where I was riding that day, that’s the tradeoff involved. There’s really nothing I could think of to get around this problem. So, for now, it’s at Curve #4 until I find a viable alternative. One solution may be the return of non-winterized fuel, which may relieve some of the pinging and allow a more aggressive curve. We’ll see…
Single-Fire vs. Dual-Fire Impressions: I was very anxious to test this out, having heard and read so much about the supposed benefits of single-fire ignition. For those of you who want to read up on this, go to HEAVY DUTY CYCLES and read Donny Petersen’s technical articles on the subject. Anyway, since they were installed simultaneously, it’s hard to say which changes in the engine’s running characteristics are due to the heads and which are due to the ignition, but here’s what I found after conducting test rides in both single-fire and dual fire modes: The idle is noticeably smoother and steadier in single-fire mode – not as lumpy as the familiar dual-fire “potato-potato” sound. It’s more of a clean, even “chug-chug” sound. Also, under no load, throttle response is much more sensitive in single-fire mode. It’s almost as if the engine got a jolt of caffeine! However, once underway, there is very little (if any) difference between the two modes. In fact, I’d be hard pressed to tell which mode the module was in while actually riding the bike! Now, I’m sure that single-fire is in some ways superior to dual-fire, and the proof is in the pudding – All the new TC88s and the high-performance XL Sports have single-fire ignition. My point is, it’s really hard to tell the difference, seat of the pants, at anything other than idle or no-load. In this case, YMMV (no pun intended). Nevertheless, I left the module set in Single-Fire mode permanently.
Other Settings and Additions: Since I rarely rev the engine past 4,500 rpm, I left the redline at the lowest setting, 6,000 rpm. And, since I don’t have any Nitrous Oxide or Turbo Kits (…yet…) I left the VOES switch in Normal mode. These two choices are obvious, based on the owner’s specific application. The ignition system was topped off with 2 pairs of Accel’s Black 8.8 mm Suppression Core Spark Plug Wires and 2 pairs of S/E’s high-performance Split-V electrode spark plugs.
Carburation Issues: Adjusting the carburation was also necessary in this case to reduce pinging. The bike was returned from the shop with the clip on the needle moved from the (original) middle position up one notch, leaning out the mixture. This was a baseless change, proven by a “hot-plug” read which showed bone-white plugs. The clip was moved back to its original spot, and this change alone helped to significantly reduce WOT / heavy-load pinging. As a further experimentation, I replaced the original 175 Main Jet with the 185 which originally came with my Yost Power Tube. This change helped to moderately reduce pinging even further. I performed a “hot-plug” read with the 185 and did not notice anything alarming, although it is a tad on the rich side. The idea of increasing the jet size was brought on in realization that my engine now closely resembles a Stage I Sportster Sport’s, and those engines generally use larger size jets than those found in standard Stage I Sportster mills. I still have to permanently finalize the jet size, but I think I’m sticking with the 185. So far, so good…
Choosing the S/E Dual Plug Heads: These heads essentially bump the compression ratio up to 9.8:1, and flow approximately 8% more than stock on both the intake and exhaust, according to HD’s Parts and Accessories Guide. They are not the ultimate in bolt-on performance – currently the Thunderstorm Heads / Pistons are, netting between 80-85 HP / 75-80 lb./ft. at the rear wheel. My setup, although not yet dynoed, probably makes approximately 75 HP / 75 lb./ft. Yet, I chose these S/E heads because they are more suitable to my style of riding than the Thunderstorms. The rule of thumb here is that generally speaking, an engine that has radical high-rpm cams is less prone to compression-induced detonation than the same engine fitted with mild low-rpm or “torque” cams, such as I have. I like my power delivery in the low and mid range, specifically under 4,000 rpm, and I have Andrews N2 cams to help accomplish this. The N2s are low-rpm “torque” cams, with relatively short duration, and they develop a relatively high cranking pressure. This cranking pressure, combined with high-compression single-plug Thunderstorm heads, would have almost certainly lead to major pinging problems. Conversely, a high rpm cam, such as S/E’s own bolt-ins, have longer intake / exhaust duration and overlap, and they develop a relatively low cranking pressure, thus minimizing pinging but moving the power delivery further up the rpm range. Since swapping out the cams and changing the delivery characteristics of the engine was not in my best interests for this project, I opted for the S/E heads. Their dual-plug design offsets some of the potential detonation problems associated with high compression applications, so much so that I was able to keep the N2 cams – which I would have never been able to do with single-plug Thunderstorms. In summary, although Thunderstorms develop substantially more horsepower (and slightly more torque) than my current setup, they do so way up in the rpm range, where I rarely go. Thunderstorms can barely tolerate Andrews N8 cams, and are more suited to more radical (high-rpm) cams, such as the aforementioned S/E bolt-ins. Therefore, these S/E heads were the only cost-effective bolt-on solution I could find for my specific application. A good reference guide for this type of motor building is Buzz Buzzelli’s aforementioned “Harley-Davidson Sportster Performance Handbook,” which helps to explain the compression / cranking pressure factor in great detail.
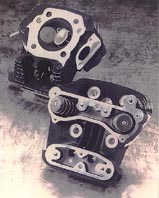
HD Press Photo of Screamin’ Eagle Heads Circa 1998
Out On The Road – Initial Driving Impressions: So what’s it like to drive now? Acceleration is significantly improved, especially over 3,000 rpm. The bike is vicious in the lower gears, tearing through them with its prodigious mid-range torque. The sound is also much more aggressive than before – it’s a really angry growl now, instead of the loud potato-potato of the old setup. I’m actually surprised at how much different the sound is – I didn’t expect it to change that much. Out on the highway, the difference in passing power is reasonable, but not as dramatic as the improvement in lower-gear acceleration. Vibration at speed is unchanged – I was disappointed, because MCN reported a huge improvement in smoothness when they tested the SE single-plug heads, and I was kind of expecting the same. Another difference I noticed is the more defined nature of the power pulses of the engine, due to the high compression. At low speeds, you can actually feel each of the engine’s completed cycles as a strong individual tug on the drivetrain, whereas before it wasn’t this way. Likewise, the starter struggles a bit more than before to turn the motor over. In addition, fuel economy seems to be slightly off, mostly due to the 185 Main Jet and my abusive test riding. It should be back to normal (40-45 mpg) once I back off it a bit.
The Future – Dyno Run and Dyno Tune: Obviously, there are quite a few variables that are involved in fine tuning this engine, and I still have some more work ahead of me before it is spot-on perfect. Then, there are the questions of how much power it actually makes, and where it makes it. For this, I plan to take the bike in for a professional dyno tune at a reputable establishment sometime in the coming month(s). At that point, I will dyno it and see how far off my estimates are. Naturally, I will post the results here. Stay tuned….
UPDATE – Dyno Tune / Results – OCTOBER 2000: Although it rarely happened before the switch, my bike developed a pinging problem after the S/E Dual-Plug heads were installed in February 2000. The problem got slightly worse after the Thunderheader was added in May 2000. After fiddling with the bike for a few months, my guess was that the high cranking pressure of the N2 Cams were incompatible with the High-Compression S/E Heads. So I decided to swap the N2s for some longer-duration cams in order to bleed off some of those effects. The logical choice was Andrews own N4 cam, which is very similar to the S/E “bolt-in” cam set. I swapped the N2s for N4s in mid-October, and as it turns out, the pinging was actually worse after the N4 cams were added in! I had checked and double checked every obvious cause, from ignition to carburation, with no relief. I threw my hands up in frustration, ready to give up.
I had tried everything I knew without much success, so decided to turn to a competent professional just to make sure I had not overlooked anything. I called Mr. Ken Puzio of Black Hills Custom Parts in Rockaway, NJ and set up a dyno tune. The final results were:
Max Horsepower = 72.2 @ ~5,600 rpm
Max Torque = 72.4 @ ~4,400 rpm
Compression Test = 175 PSI, Front and Rear
CLICK HERE FOR THE DYNO CHART (This chart shows the bike with a 220 main jet. It had slightly higher numbers with the 210 main jet, but pinging was worse).
Now to the fun stuff – this tune was less about power than making the bike run correctly. With the N4s in, the pinging was awful, from mid-throttle in 2nd gear onwards. After the tune, the bike still wasn’t running correctly – but it was much better than before. The bike was drivable again, so long as I didn’t push much past half throttle in gears 3-5, else pinging reared its ugly head. I could still get the bike to ping in 2nd, but not as badly as before. To source the problem, Mr. Puzio checked a variety of factors, including-
1. VOES– It is wired correctly and working, but it aggravated the pinging problem. We had good results on the street with it disconnected. Dyno numbers were not significantly affected with it off, so we left it OFF – for now.***
2. Carburation– The new 5/16″ fuel line is unobstructed. Even with my 200 main, the bike seemed to stave for fuel. We the Yost Power Tube in place, we bumped up to a 210 and then to a 220 (!!) with good results. Horsepower and Torque increased, and pinging decreased. This was a band-aid solution, however, covering up the real problem (as described below).
3. Running with 2 plugs instead of 4– No significant change.
4. Swapping the Yost Power Tube for a generic jet kit– No significant change.
5. Check Coil Operation & Spark Plug Wiring– OK
6. Checking Timing (dynamic)– OK. About 40 degrees with VOES on, about 30 with VOES off.
7. Check Hall Effect plate– OK
8. Clean Air Filter– OK
***FINAL UPDATE ***A conversation with Mr. Brian Nallin of Nallin Racing Head Service in the Spring of 2001 revealed one more factor which was overlooked the whole time. The pinging problem was most likely the VOES adjustment. The VOES was never adjusted to deal with the high compression configuration my motor was in – rather, it was left in the stock XL position of 3.5″. Adjusting this upward to 6.5″ would most likely have eliminated the pinging problem.